Augmented Reality in Manufacturing & Factory Operations
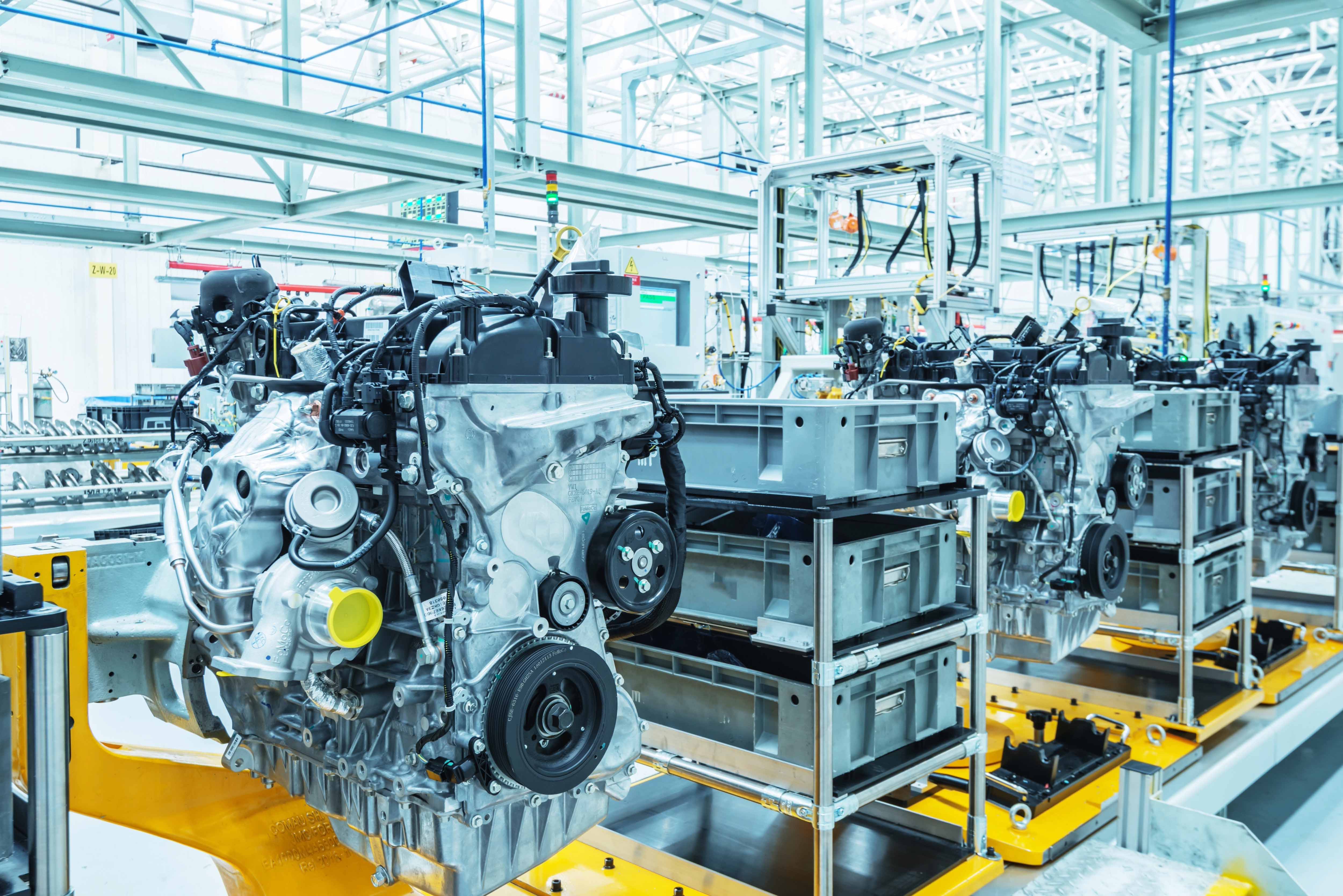
Reshaping Production Facilities with Remote Support & AR Workflows
From optimizing machinery installation to enhancing equipment maintenance and operator training, AR Genie leverages cutting-edge Augmented Reality technology to provides immersive, real-time assistance, driving efficiency & precision in factory operations.
.jpg)
Transforming Manufacturing with AR Technology
Digitize manufacturing work instructions & assembly processes for training. Optimize equipment manufacturing process & productivity with extended expert support for smooth operations, maintenance, inspections, & repair on the factory floor with AR technology.
.jpg)
Revolutionize Factory Floor with Faster Training & Issue Resolution
In manufacturing, efficiency and precision are essential. Downtime due to machinery breakdowns or unclear workflows can disrupt production lines and negatively affect output. AR Genie Remote & Work Assist transforms how frontline workers and equipment operators receive support, improving job performance and accuracy.
.jpg)
Benefits of Augmented Reality in Manufacturing
Enhance Shop Floor Maintenance
With AR-powered devices like smart glasses or handhelds, remote experts can see the shop floor in real-time from the perspective of on-site technicians. AR Genie allows experts to overlay annotations and highlight specific components, guiding workers through complex tasks for more accurate, efficient maintenance and repairs.
Minimizing Production Disruptions & Equipment Downtime
AR Genie’s real-time support and remote inspection capabilities improve first-time fix rates, minimizing disruptions caused by machinery breakdowns. Remote experts can troubleshoot issues before they become critical, leading to reduced production delays and maximizing operational uptime.
Streamlining Factory Equipment Installation
Installing complex machinery is often expensive and time-consuming, especially when experts are not present on-site. AR Genie’s Remote Assist enables real-time communication and guidance, helping on-site personnel overcome installation challenges. This reduces installation costs and accelerates the process with faster issue resolution.
Step-by-Step Manufacturing SOPs with Digital Workflows
Paper-based Standard Operating Procedures (SOPs) can be prone to misinterpretation. AR Genie offers digital AR-guided instructions, transforming workflows into clear, visual step-by-step processes. Workers can access AR overlays and manuals, ensuring faster, more accurate maintenance and inspections, improving equipment uptime and operational efficiency.
.jpg)
Key Use Cases for AR in Telecom
Improved Network Optimization & Maintenance
Our Smart Voice Assistance allows aerospace professionals to access critical data hands-free, minimizing manual interactions and distractions for engineers and ground personnel. This feature supports interactive training and provides immediate access to manuals, schematics, and troubleshooting guides, ensuring faster and more accurate repair processes.
Training & Onboarding
AR, combined with 3D models and digital twins, transforms aerospace maintenance by offering immersive training experiences and enhanced workflows. Real-time visualization through AR enables accurate diagnosis and smoother repair processes, while 3D models and digital twins allow for interactive and effective training, ensuring efficiency and safety.
Customer Service & Support
AR-powered customer service solutions enable faster troubleshooting and device setup, offering a more personalized and efficient support experience for telecom customers.